Cost estimation in the realm of brownfield petrochemical projects is both an art and a science. Unlike greenfield projects, where the site is essentially a blank canvas, brownfield projects require careful consideration of existing infrastructure, environmental concerns, and operational constraints. The process is complex, involving multiple variables that can significantly impact the overall cost.
Understanding Brownfield Projects
Before diving into the cost estimation process, it’s essential to understand what a brownfield project entails. Brownfield projects involve the redevelopment or expansion of an existing facility. In the petrochemical industry, this often means upgrading or modifying existing plants, pipelines, or storage facilities. Unlike greenfield projects, where everything is built from scratch, brownfield projects require careful planning to integrate new developments with existing structures.
Brownfield projects come with their own set of challenges, including:
- Integration with Existing Infrastructure: The new developments must seamlessly integrate with the existing infrastructure, which may be outdated or in poor condition.
- Environmental Concerns: Brownfield sites may be contaminated with hazardous materials, requiring extensive remediation efforts.
- Regulatory Compliance: Brownfield projects must comply with stricter environmental and safety regulations, which can add to the cost and complexity of the project.
Given these challenges, accurate cost estimation is critical to the success of brownfield petrochemical projects.
The Importance of Cost Estimation
Cost estimation is a crucial step in the planning and execution of any petrochemical project. Accurate cost estimates help project managers make informed decisions, secure financing, and allocate resources efficiently. Inaccurate estimates, on the other hand, can lead to cost overruns, delays, and even project failure.
For brownfield projects, the stakes are even higher. The complexity of integrating new developments with existing infrastructure, coupled with the need to address environmental and regulatory concerns, makes cost estimation a particularly challenging task. However, with the right approach and tools, it is possible to develop accurate cost estimates that account for these variables.
Steps in Cost Estimation for Brownfield Petrochemical Projects
The process of cost estimation for brownfield petrochemical projects typically involves several key steps:
-
Project Definition and Scope Identification:
- Scope Definition: Clearly defining the project scope is the first and most crucial step in cost estimation. This involves identifying the specific goals of the project, the tasks required to achieve these goals, and the resources needed. In brownfield projects, scope definition is more complex because of the existing infrastructure and operational constraints.
- Feasibility Studies: Conducting feasibility studies is essential to determine whether the project is viable from both technical and economic perspectives. These studies help in identifying potential risks, challenges, and opportunities, which in turn inform the cost estimation process.
-
Site Assessment:
- Thorough Assessment: For brownfield projects, a thorough site assessment is critical. This includes evaluating the condition of existing infrastructure, identifying potential environmental hazards, and assessing the impact of the project on ongoing operations. The results of the site assessment play a significant role in determining the cost of the project.
- Environmental Remediation Costs: If the site assessment reveals contamination or other environmental issues, the cost of remediation must be factored into the overall estimate.
-
Design and Engineering:
- Detailed Engineering Plans: The design phase involves developing detailed engineering plans for the project. This includes everything from process design and equipment selection to layout and structural design. In brownfield projects, the design must account for the constraints imposed by the existing infrastructure.
- Front-End Engineering Design (FEED): FEED is a critical component of the design phase that provides detailed cost estimates for the project. It involves developing a more refined project scope, identifying long-lead items, and estimating the cost of materials, labor, and equipment.
-
Cost Data Collection:
- Collection Process: Collecting accurate cost data is essential for developing reliable cost estimates. This includes data on material costs, labor rates, equipment costs, and subcontractor fees. For brownfield projects, historical data from similar projects can be particularly valuable.
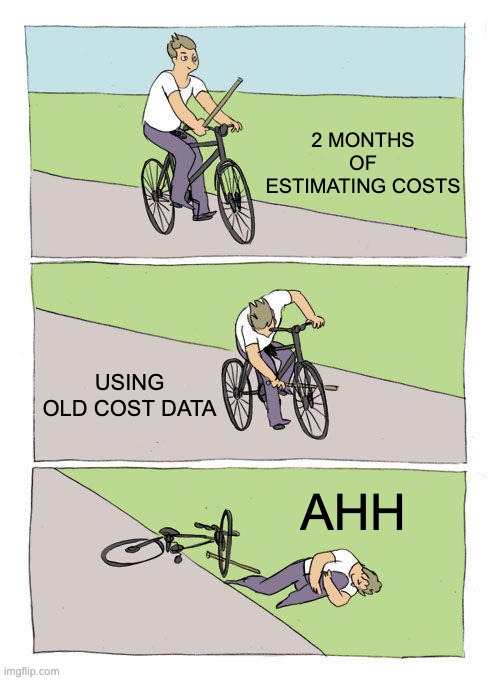
- Benchmarking: Comparing the project with similar projects can help validate cost estimates and identify potential cost-saving opportunities.
-
Risk Assessment and Contingency Planning:
- Risk Assessment: Risk assessment is a critical step in the cost estimation process. This involves identifying potential risks, such as delays, cost overruns, or safety incidents, and developing contingency plans to mitigate these risks. In brownfield projects, risks are often higher due to the complexity of integrating new developments with existing infrastructure.
- Contingency Allowances: Based on the risk assessment, contingency allowances should be included in the cost estimate to account for unforeseen events or changes in project scope.
-
Cost Estimation Methodologies:
Several methodologies can be used for cost estimation in brownfield petrochemical projects, including:
- Analogous Estimation: This method involves using historical data from similar projects to estimate costs. It is particularly useful in the early stages of a project when detailed information is not yet available.
- Parametric Estimation: This method uses statistical relationships between project variables (e.g., size, complexity, and cost) to develop cost estimates. Parametric estimation is often used in conjunction with other methods to refine cost estimates.
- Bottom-Up Estimation: This method involves estimating the cost of individual tasks or components and then summing them to develop the overall project cost. Bottom-up estimation is more accurate but also more time-consuming.
- Three-Point Estimation: This technique involves estimating three possible scenarios – best case, worst case, and most likely case – and calculating the weighted average to get a more realistic estimate.
-
Review and Validation:
- Consider All Factors: Once the cost estimate has been developed, it should be reviewed and validated by key stakeholders, including project managers, engineers, and financial analysts. This helps ensure that the estimate is realistic and accounts for all relevant factors.
- Independent Estimation Review: Engaging a third party to review the cost estimate can provide an unbiased assessment and identify any potential gaps or inaccuracies.
-
Final Cost Estimate and Budgeting:
- Final Cost Estimate: After the review and validation process, the final cost estimate is developed, and the project budget is established. The final estimate should include all direct and indirect costs, as well as contingencies for risks and uncertainties.
- Cash Flow Analysis: In addition to the overall cost estimate, a cash flow analysis is essential to ensure that the project has sufficient funding at each stage of development.
-
Monitoring and Updating:
- Frequent Monitoring: Cost estimation is not a one-time activity. Throughout the project, costs should be monitored and compared against the original estimate. If there are significant deviations, the estimate should be updated accordingly.
- Change Management: Implementing a robust change management process is essential for controlling costs in brownfield projects. Any changes to the project scope, design, or schedule should be carefully evaluated and their impact on costs should be assessed.
Challenges in Brownfield Project Cost Estimation
While the process outlined above provides a structured approach to cost estimation, brownfield petrochemical projects come with unique challenges that can complicate the process:
-
Unknowns and Uncertainties: Brownfield projects often involve dealing with unknowns, such as the condition of existing infrastructure or the extent of environmental contamination. These uncertainties can make it difficult to develop accurate cost estimates.
-
Integration Complexity: Integrating new developments with existing infrastructure can be a complex and costly process. Ensuring that the new systems work seamlessly with the old ones often requires significant engineering effort and can lead to unexpected costs.
-
Regulatory and Permitting Delays: Brownfield projects are subject to stringent regulatory requirements, which can lead to delays and additional costs. Navigating the permitting process can be time-consuming, and any changes in regulations can impact the cost and schedule of the project.
-
Operational Constraints: In many brownfield projects, the existing facility remains operational during the construction phase. This can create additional challenges in terms of safety, logistics, and scheduling, all of which can impact costs.
-
Market Volatility: Fluctuations in the cost of materials, labor, and equipment can also pose a challenge for cost estimation. In the petrochemical industry, market conditions can change rapidly, and these changes can have a significant impact on project costs.
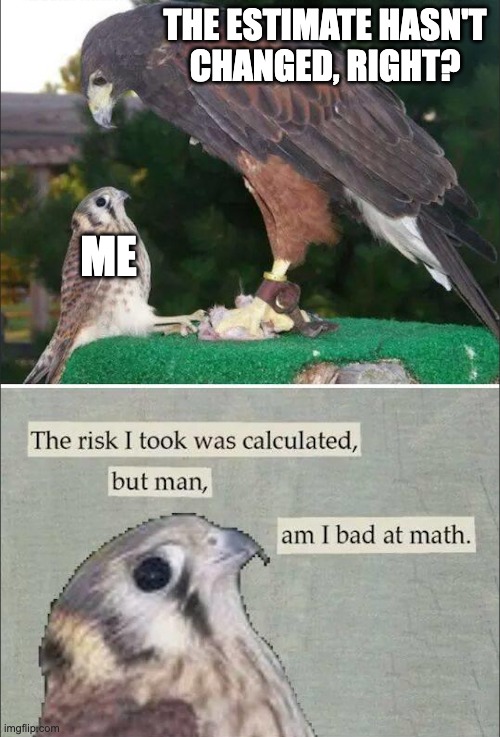
Best Practices for Cost Estimation
To overcome these challenges and develop accurate cost estimates for brownfield petrochemical projects, consider the following best practices:
-
Engage Experienced Estimators: Cost estimation for brownfield projects requires specialized knowledge and experience. Engaging estimators with a deep understanding of the petrochemical industry and brownfield projects can significantly improve the accuracy of the estimate.
-
Leverage Technology: Advanced software tools can help streamline the cost estimation process by providing accurate data, modeling scenarios, and facilitating collaboration among stakeholders. Tools such as Building Information Modeling (BIM) and cost management software can be invaluable in brownfield projects.
-
Collaborate with Stakeholders: Effective collaboration among all project stakeholders – including engineers, contractors, regulators, and financial analysts – is essential for accurate cost estimation. Regular communication and feedback can help ensure that all factors are considered and that the estimate is realistic.
-
Conduct Regular Reviews: Regularly reviewing and updating cost estimates as the project progresses can help identify potential issues early on and prevent cost overruns.
-
Plan for Contingencies: Given the uncertainties inherent in brownfield projects, it is essential to include contingencies in the cost estimate. This provides a buffer for unexpected events and helps ensure that the project stays within budget.